KEW Foundries manufactures some of the largest slag pots and chill moulds on the African continent, ideal for small and large melting and smelting applications. KEW Foundries has been involved in the foundry and engineering industries for over 100 years and has the industry know-how and expertise to execute challenging projects all the way from pattern design and fabrication through to manufacture and delivery.
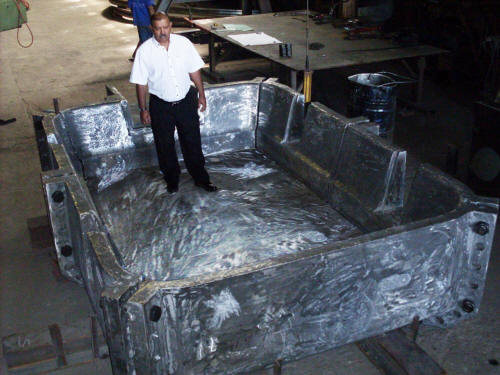
KEW Foundries has manufactured slag pots from 300 kg to 5.5 tonnes
“At KEW Foundries we have the ability to manufacture single piece slag pots and chill moulds up to a total weight of seven tonnes. However, larger chill moulds and slag pots can be manufactured in part assemblies which also reduce the cost of transportation. In this case there is no tonnage or size restriction on the solution that we can supply,” says John Bryson, Foundry Director, KEW Foundries.
To date, the company has manufactured chill moulds with weights from 20 kg up to 26 tonnes and slag pots from 300 kg to 5.5 tonnes. However, the company has the infrastructure and the technological expertise to fabricate larger products to client specifications.
Slag pots and chill moulds are manufactured from either heat resistant cast iron or SG iron, to provide long-lasting quality solutions and are suited to various processes which include lead, aluminium, iron, steel, chrome, manganese, copper and many other smelting applications.
KEW Foundries’ design department advises and collaborates with clients to achieve designs suited to specific applications. The company has an extensive pattern library, as well as the facilities and expertise to design, manufacture and store unique client patterns. “For years we have delivered customised solutions designed specifically to client specifications,” says Bryson.
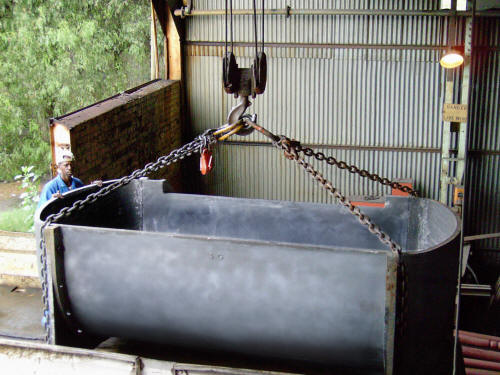
Chill moulds are manufactured from either heat resistant cast iron or SG iron to
ensure long-lasting quality
KEW Foundries ensures that quality standards are maintained, using laboratory facilities equipped with modern equipment, including an ARL 3460 Ret B optical emission spectrometer, a metallographic section and a sand testing section. The company conducts non-destructive testing in-house using magnetic particle, die-penetrant and ultrasonic testing methods, to ensure that clients receive quality products free of defects. Physical testing of products is presently conducted by an independent laboratory.
“By conducting thorough testing of both our materials and our products we can ensure that our clients have access to not only dimensionally suitable slag pots and chill moulds, but also the highest quality standards,” explains Bryson.